Available Surface Finishes
Deburr/Mill
A burr is a raised edge or small piece of material remaining attached to a piece after production. Milling is the process of removing the burrs. Your part will be supplied with no finishing, other than removal of burrs.
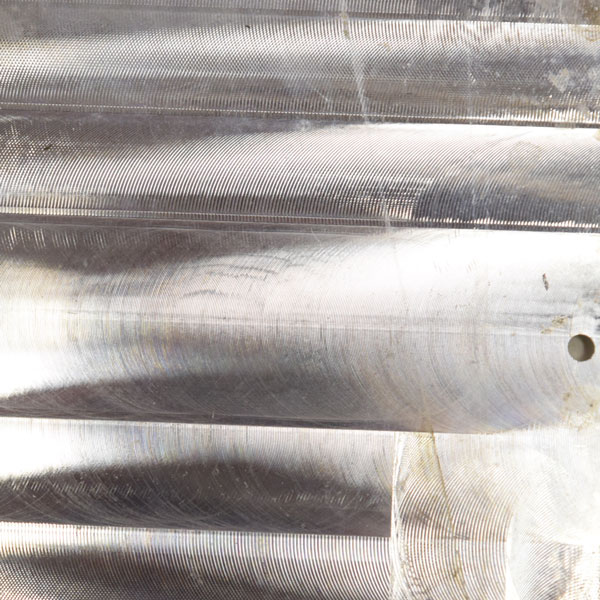
Rough Polish
The part is to be supplied with a rough polish which will remove most machining marks. Some scratches and machining marks still may remain. These minor scratches can be removed with high grit wet sanding followed by polishing.
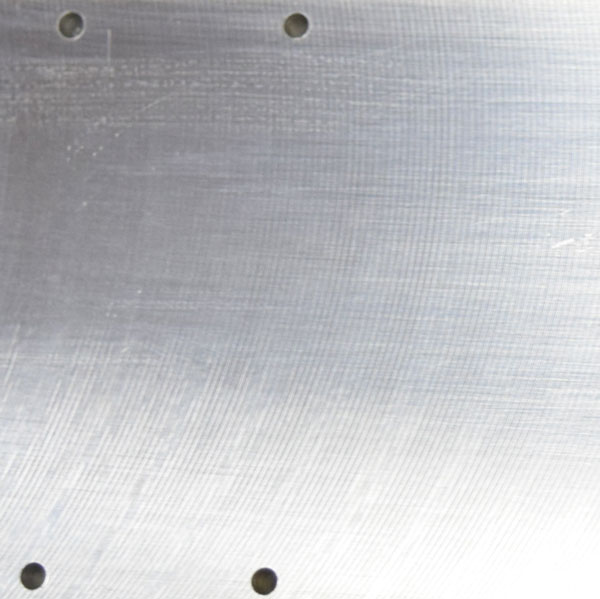
Bead Blast
Bead Blasting uses glass beads at a high pressure to provide a certain finish. Light bead blasting may produce a satin finish, where heavy bead blasting results in a matte finish. Standard bead blasting uses 80#. Your part will be supplied with a consistent dull finish.
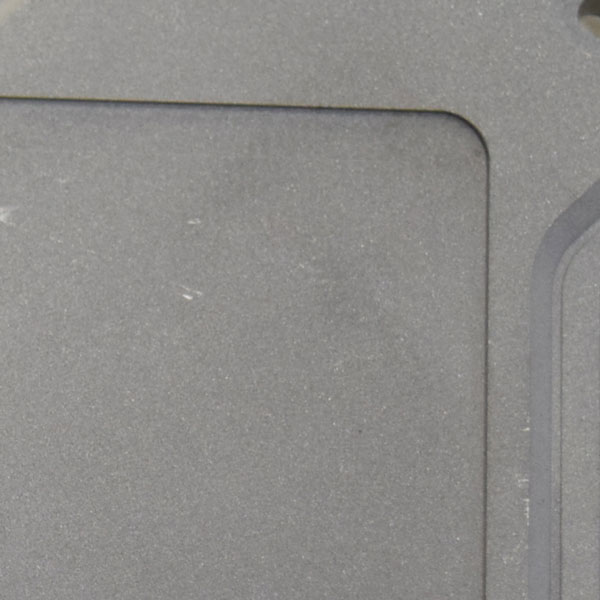
Knurling
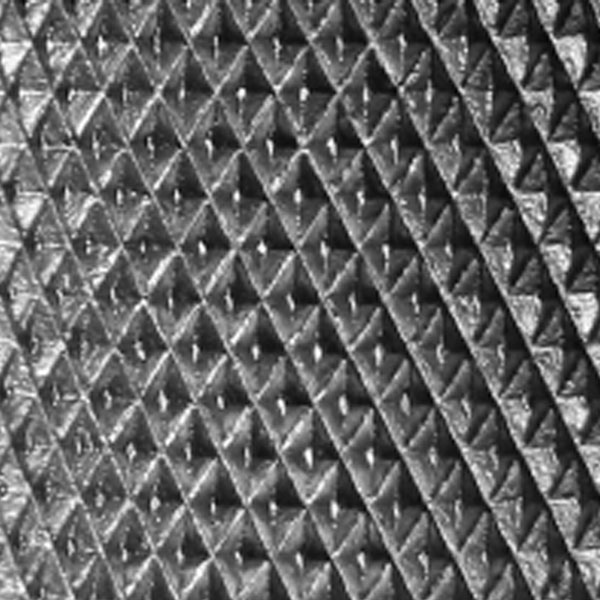
Brushing
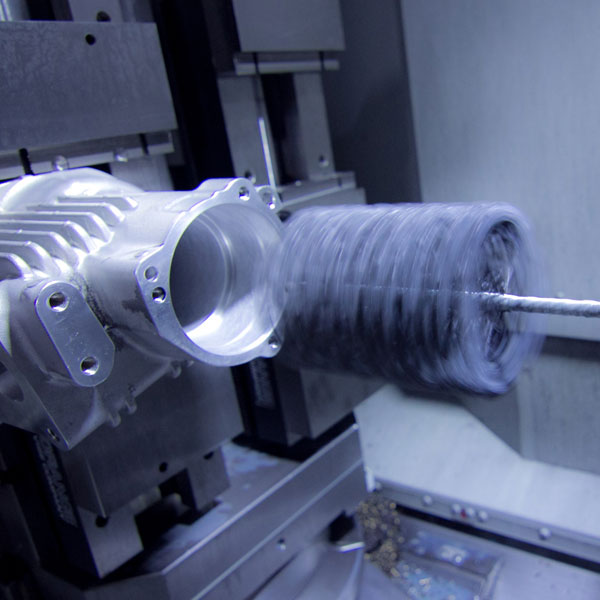
Tumbling
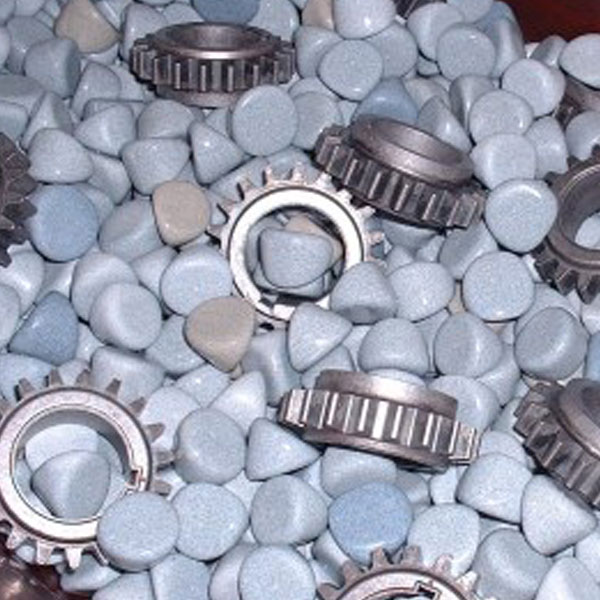
Available Surface Treatments
Anodizing
Sulfuric Anodize MIL-A-8625/Type II
Type II, Class 1 ; Type II, Class 2
Hard Anodize MIL-A-8625/Type III
Type III, Class 1 ; Type III, Class 2
Anodizing creates a thin oxidized layer that may be dyed a certain color. Anodizing is only available on Aluminum or Stainless Steel materials. Anodizing will make the surface non-conductive. Type I thin or Type III thick anodizing is available. Colors include: Clear, Black, Red, Blue, Orange, Purple, Green, and Brown.
Chromate Conversion/Alodine
MIL-DTL-5541 ; Hexavalent Yellow and Trivalent Clear
Type I, Class 1A ; Type I, Class 3
Type II, Class 1A ; Type II, Class 3
Chromate Coating provides additional corrosion resistance or as a primer for powder coating while maintaining conductivity. Chromate coatings are soft and gelatinous when first applied, but harden and become hydrophobic as they age. This process creates an iridescent or yellow tint to the part.
Electropolishing
ASTM-B-912
One of the benefits of electropolishing for stainless steel, is that it removes iron from the surface and enhances the chromium/nickel content. This process creates a mirror like finish on the part, creating a higher polish than what can be created manually. Surface quality obtained by Electropolishing is directly related to the quality of the pre-electropolished surface. Electropolishing cannot remove digs, gouges, scratches or other similar surface distortions.
Passivation
ASTM A967, AMS2700, ASTM A380
Passivation uses a nitric or citric acid to create a protective oxide layer on parts made from austenitic, ferritic, and martensitic corrosion-resistant steels. The protective layer helps improve the corrosion resistant qualities of the metals.
Nickel and Silver Electroplating
Electroplating adds a thin layer of metal onto another metal object. The plated layer can be decorative, provide corrosion resistance, wear resistance, or used to build up worn or undersized parts for salvage purposes.
Ceramic Coating
We offer various brands of ceramic coating. Cerakote (H-240) is a Polymer-Ceramic Composite ceramic coating that can be applied to metals, plastics, polymers and wood. The unique formulation used for Cerakote ceramic coating enhances a number of physical performance properties including abrasion/wear resistance, corrosion resistance, chemical resistance, impact strength, and hardness.
Black Oxide
MIL-DTL-13924
Class 1
Class 4
Black oxide or blackening is a conversion coating for ferrous materials, stainless steel, copper and copper based alloys, zinc, powdered metals, and silver solder. It is used to add mild corrosion resistance, for appearance and to minimize light reflection. To achieve maximal corrosion resistance the black oxide must be impregnated with oil or wax. One of its advantages over other coatings is its minimal buildup.
Dow 9
MIL-M-3171C/Type IV
A galvanic anodize treatment for magnesium. Produces a dark brown to black coating. Designed to give a protective film on alloys which do not react to Dow No. 7 treatment.
Dow 7
MIL-M-3171/Type III
Chemical treatment No.7 (dichromate) is a chemical dip conversion coating and is most commonly used for magnesium and its alloys. The applied coatings may vary from light to dark brown, with no appreciable dimensional change, normally applied after machining and before painting.
Laser Engraving
Need special markings engraved? We offer laser engraving. Inquire to learn more.
Surface Roughness
Below is a comprehensive table to the different levels of surface roughness and their regional conversions.
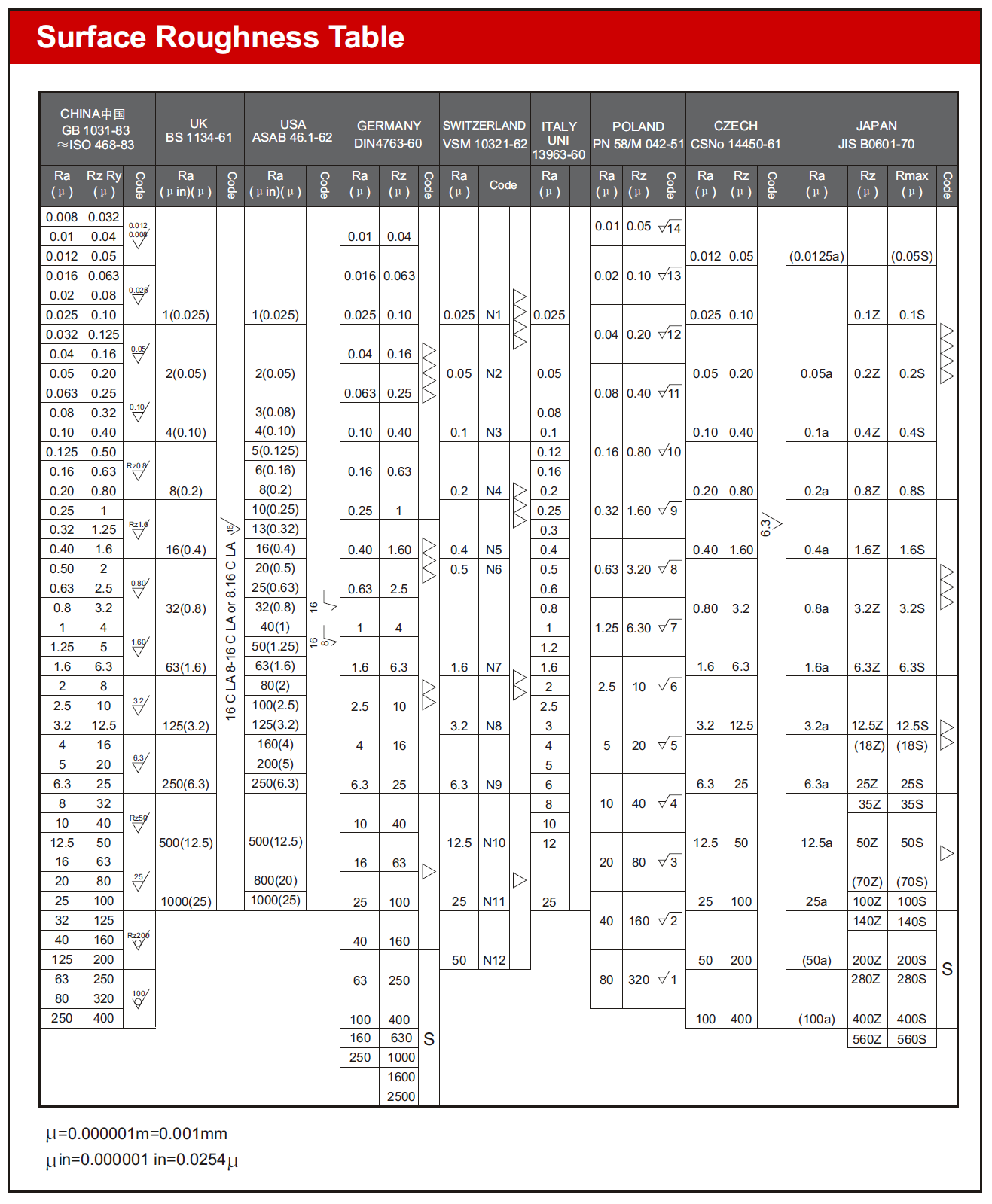
Accelerate Your Innovation
We’re here to help you manufacture your machined parts efficiently and timely. We understand the importance of getting your product(s) to market before your competitors do. We provide quotes in hours and most parts in 14-Days or less. Use the form to reach our specialists to request a quote, check on an order status, or to learn more about us and our capabilities. We’re ready to accelerate your innovation.